In an environment where production speed is becoming more important and efficiency while being economical is a driver for manufacturers, acknowledging the significance of dwell time in tablet production is a must. How to dwell time impacts tablet manufacturing and reveals the new technology that may help with the production process.
- Many tablet formulations are dwell-sensitive and require more time under compression to ensure they come off the press without any faults. In tablet compression, dwell time is the time that the punch head remains in contact with the compression roller. It is defined as the amount of time that the compression force applied when forming the tablet is above 90% of its peak value.
- Some granules are extremely difficult to compress effectively and require extended time under peak compression to obtain the required tablet hardness and prevent any difficulties like sticking, one of the most frequent and challenging problems in tablet manufacture. Sticking is the build-up of granule on the punch tip face, this leads to tablet press downtime and reduced tablet output. Quite often to solve the problem, the press speed is reduced or a higher compression force is applied. Both these solutions can solve a sticking issue but can also cause other issues such as lower productivity and a longer dissolution time due to the increased tablet hardness.
- It is not just sticking that can cause production problems, capping and delamination may also be an issue. Trapped air pockets in the forming tablet can cause severe problems during manufacture. If the air is insufficiently squeezed out and/or density variations occur in the tablet volume, the tablet tensile strength is negatively affected and the risk of tablet capping or delamination increases.
- One of the most effective methods to reduce the risk of air entrapment is to extend the dwell time to expel air from the tablet, alternatively tapered dies can be used or the press can be slowed down but this again has a negative effect on production rates.
What is Dwell time?
- The dwell time of tablet compression is the time for which the tablet punch head remains in contact with the compression roller. That means the duration of time that the compression force is applied when forming the tablet.
How it is helpful?
- The Dwell Time Calculation helps to understand how long your tablet is under maximum compression.
- This will help during the scale-up of the batch from small-scale R&D to batch production scale.
- The longer the dwell time, the harder the tablet will become. This is because the energy created when compressing the tablets has time to dissipate and does not allow for the elasticity of the powders to spring back.
ALSO READ: What is Maximum Compression Force?
The formula for dwell time calculation
Where:
dt = Dwell Time (milliseconds)
Dhf = Head Flat Diameter (millimeters)
Dpc = Pitch Circle Diameter of Turret (millimeters)
rpm = Revolutions per Minute (turret speed)
- Dwell time expressed in milliseconds is the time in which the punches achieve maximum penetration in the die under the main compression rollers and the punches are no longer moving vertically.
- In other words, dwell time occurs when the compression rollers are in contact with the punch head flat. Dwell time is a contributing factor to the tablet's strength and a means for product transfer from one tablet press to another.
- Although turret RPM or tablets-per-minute are a common language for the turret speed, it doesn’t allow a true comparison for tablet presses with different turret sizes but the turret velocity is a normalization of turret size and the dwell time is a normalization of the turret size and punch head flat. It is important to
- understand the turret velocity before we can discuss dwell time.
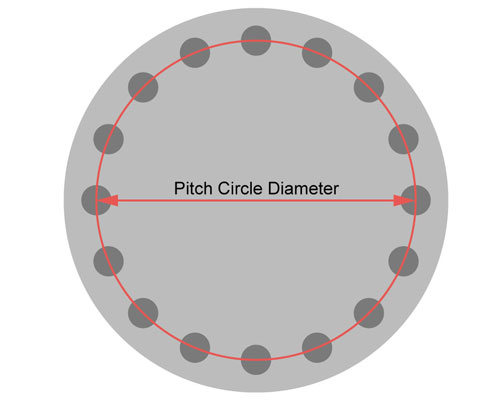
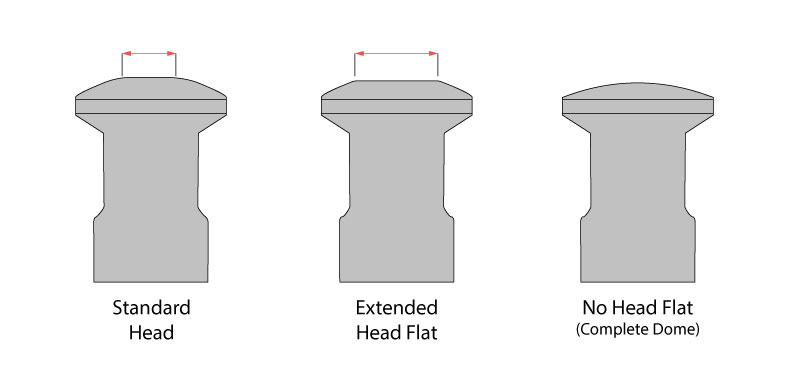
ALSO READ: Types of Tooling in Compression Machine
Tags
Production